Jim McConkey wrote:And I believe you post up to three images per messages now.
Lets check...
So, I bit the bullet and broke out the sister back...
After going through the same procedure as with the first back, I got this
The new and the old together. In the picture, the figure in the first one looks nicer, but they are actually quite similar
Scraped and sanded smooth
Marking the limit of the inside curvature by tracing the edge of the linings onto the back plate
Drilling out much of the waste with forstner bit in the drill press. There is a smooth headed bolt directly under the spindle, and the depth stop is set at a fixed distance from it. This leaves the remaining wood at a uniform thickness, and a good starting point for graduating
Result
After hogging most of the rest of the waste out with a gouge, a carving spoon is used for some coarse carving
Next step is planing with small finger planes. My favourite ones are shop made
When I get close to final dimensions, I use this simple thickness gauge to monitor my progress.
Finally, everything is scraped and sanded smooth
After repeating the procedure for the inside of the top plate, it is time to cut the f-holes. I use a template to trace the onto the outside of the top. A small hole is drilled in its largest eye, and a fine coping saw blade is inserted, before sawing just inside the lines. I try to keep the walls in the holes vertical, by sawing straight through a hole in a little workboard clamped to my regular bench.
I find I get the cleanest results by paring the rest of the way with a violin maker’s knife. You have to pay attention to the grain direction, and the knife must be quite sharp, of course.
This is one of the most enjoyable tasks in the whole building process for me, so here’s one more
To shape the eyes, some sand paper wrapped around a pencil works fine
Finished f-hole
Recording the finished graduations, weight etc for future reference.
Tracing the inside curvature onto the side of a quartered, split piece of red spruce.
Planing and scraping most of the waste away, before final “chalk fitting”. When there is even transfer of chalk between the mating surfaces, it is ready to be glued in place. The chalk is sanded off with 220 grit sand paper
Gluing the brace with hot hide glue, and multiple clamps for even pressure.
Paring the braces down, before rounding them over and sanding everything smooth.
Gluing the top to the rim in the go-bar deck
Result
The neck blank, squared up. Checking the optimal cut with the neck template...
Cutting out the neck blank on the small band saw
Cutting the truss rod slot on the table saw. I small shim is temporarily glued to the nut end, so the bottom of the slot will be at an equal distance from the back of the finished neck, which tapers in thickness.
Gluing on peghead “ears” from the cut-offs
I didn’t have any more 5 mm bar stock left, but rummaging my drawers I found I could make an ordinary tension rod by canibalizing this Stewmac “hot rod”. Luckily, one end has the correct threads for the Gibson style brass nuts that I use. I plan to cut it to the correct length and bend the other end at an angle, to anchor it to the heel end of the neck
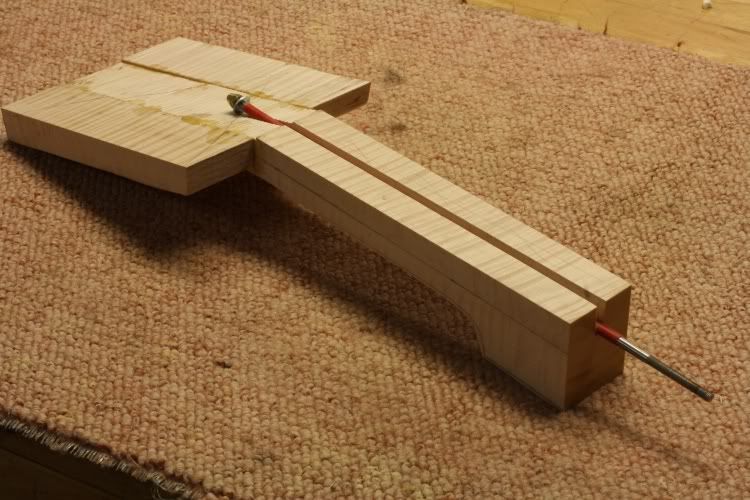