Neck-through construction geometry
-
- Posts: 1182
- Joined: Fri Jan 06, 2012 6:25 pm
- Location: San Diego, CA
Neck-through construction geometry
OK - here we go...
By my drawing, I need the plane (top surface) of the neck-shaft to be about 1/8" (3mm) above the plane of the top of the body.
I could make a thick FB, but that would be just but-tugly.
So - this sucks! I wanted to glue on the wings, and put the whole thing through the sander to get my nice flat top/back of the body ... but I can't because there will be this little rectangular pillar (or maybe "platform") required to hold up the fingerboard piece that goes over the body.
How do y'all deal with this??
Should I just sand the whole top flat, and make a separate piece that holds up the FB extension?? (that is a flat-topper's term)
By my drawing, I need the plane (top surface) of the neck-shaft to be about 1/8" (3mm) above the plane of the top of the body.
I could make a thick FB, but that would be just but-tugly.
So - this sucks! I wanted to glue on the wings, and put the whole thing through the sander to get my nice flat top/back of the body ... but I can't because there will be this little rectangular pillar (or maybe "platform") required to hold up the fingerboard piece that goes over the body.
How do y'all deal with this??
Should I just sand the whole top flat, and make a separate piece that holds up the FB extension?? (that is a flat-topper's term)
Likes to drink Rosewood Juice
-
- Posts: 2690
- Joined: Sat Jan 07, 2012 10:01 pm
- Location: Portland, OR
- Contact:
Re: Neck-through construction geometry
Chuck,
It's a pretty typical day in a neck-through maker's life. I actually glue the fingerboard on before I glue the body wings on. I then carve away the body part of the neck blank so that the fingerboard top is 3/8 proud of then body top. (Saf-t-Planers are great for this job). I also rough out the pickup cavities on the bandsaw and rout in all the wiring channels from the side before glueing the wings on.
Just sand your body wings precisely to final thickness (1-5/8") and make a dowelling jig to drill the body halves and neck blank so the your glueups are perfectly aligned. Clamping the wings is always a chore but hopefully you saved the body wing cutoffs which you will use as clamping cauls.
My dowel drilling jig is very simple, I have a 1/2" piece of baltic ply that's 12" long by 1-5/8" wide with two ball bearing races mounted where the dowel locations are. The races have a 3/8" i.d. and keep the drill centered without wearing out over time. It's yet another idea I stole from Charles Fox. I just clamp or tape the jig in place and drill away.
It's a pretty typical day in a neck-through maker's life. I actually glue the fingerboard on before I glue the body wings on. I then carve away the body part of the neck blank so that the fingerboard top is 3/8 proud of then body top. (Saf-t-Planers are great for this job). I also rough out the pickup cavities on the bandsaw and rout in all the wiring channels from the side before glueing the wings on.
Just sand your body wings precisely to final thickness (1-5/8") and make a dowelling jig to drill the body halves and neck blank so the your glueups are perfectly aligned. Clamping the wings is always a chore but hopefully you saved the body wing cutoffs which you will use as clamping cauls.
My dowel drilling jig is very simple, I have a 1/2" piece of baltic ply that's 12" long by 1-5/8" wide with two ball bearing races mounted where the dowel locations are. The races have a 3/8" i.d. and keep the drill centered without wearing out over time. It's yet another idea I stole from Charles Fox. I just clamp or tape the jig in place and drill away.
-
- Posts: 1182
- Joined: Fri Jan 06, 2012 6:25 pm
- Location: San Diego, CA
Re: Neck-through construction geometry
Thanks David!
That explains a lot - I needed a rough "order of operations" to move forward with.
And the doweling jig was a thought I had, but now it is confirmed.
That explains a lot - I needed a rough "order of operations" to move forward with.
And the doweling jig was a thought I had, but now it is confirmed.
Likes to drink Rosewood Juice
-
- Posts: 1554
- Joined: Fri Jan 06, 2012 4:05 pm
- Location: Portland, OR
Re: Neck-through construction geometry
I have yet to build a neck-through, but it'll come up eventually. I, too, like to hear the order of operations that different folks choose. Thanks, David.David King wrote:Chuck,
It's a pretty typical day in a neck-through maker's life. I actually glue the fingerboard on before I glue the body wings on. I then carve away the body part of the neck blank so that the fingerboard top is 3/8 proud of then body top. (Saf-t-Planers are great for this job). I also rough out the pickup cavities on the bandsaw and rout in all the wiring channels from the side before glueing the wings on.
Just sand your body wings precisely to final thickness (1-5/8") and make a dowelling jig to drill the body halves and neck blank so the your glueups are perfectly aligned. Clamping the wings is always a chore but hopefully you saved the body wing cutoffs which you will use as clamping cauls.
My dowel drilling jig is very simple, I have a 1/2" piece of baltic ply that's 12" long by 1-5/8" wide with two ball bearing races mounted where the dowel locations are. The races have a 3/8" i.d. and keep the drill centered without wearing out over time. It's yet another idea I stole from Charles Fox. I just clamp or tape the jig in place and drill away.
-Ruining perfectly good wood, one day at a time.
-
- Posts: 1188
- Joined: Wed May 30, 2012 11:47 pm
- Location: Edmonton AB. Canada
Re: Neck-through construction geometry
2 out of my last 3 guitars have been neck-through designs.
On the first, I used a fret board that was 9/32 thick, to get a proper height above the body. By the time it was shaped, it was only about 3/16 thick at the edge.
I ended up with enough height for the bridge, but could have used another 32nd of an inch.
The next guitar I used a fret board that is 5/16 thick. I also bound it with maple, before shaping the radius into it. The binding makes it look fairly normal.
Because the fret board was a bit thicker, and I didn't want the neck too thick, I thinned the back of the neck to 7/16.
I realize that is too thin for the 3/8 deep truss rod, so I routed the back of the fret board 1/16 deep to allow for it.
The second fret board was bound and shaped before gluing it on.
As for the body wings, I routed a channel into the bottom wing to allow for wiring. I calculate how far into the wing the pickup rout would go, and routed to that depth. The rout was placed so that it met the pickup rout at a 1 inch depth, and went from the neck pickup to the end of the bridge rout.
I used joinery biscuits on the second guitar to help with line-up.
I'm almost done with the second guitar and will post pics soon.
On the first, I used a fret board that was 9/32 thick, to get a proper height above the body. By the time it was shaped, it was only about 3/16 thick at the edge.
I ended up with enough height for the bridge, but could have used another 32nd of an inch.
The next guitar I used a fret board that is 5/16 thick. I also bound it with maple, before shaping the radius into it. The binding makes it look fairly normal.
Because the fret board was a bit thicker, and I didn't want the neck too thick, I thinned the back of the neck to 7/16.
I realize that is too thin for the 3/8 deep truss rod, so I routed the back of the fret board 1/16 deep to allow for it.
The second fret board was bound and shaped before gluing it on.
As for the body wings, I routed a channel into the bottom wing to allow for wiring. I calculate how far into the wing the pickup rout would go, and routed to that depth. The rout was placed so that it met the pickup rout at a 1 inch depth, and went from the neck pickup to the end of the bridge rout.
I used joinery biscuits on the second guitar to help with line-up.
I'm almost done with the second guitar and will post pics soon.
I need your help. I can't possibly make all the mistakes myself!
-
- Posts: 506
- Joined: Mon Feb 27, 2012 11:34 am
Re: Neck-through construction geometry
I haven't built a thru neck guitar (yet) but why wouldn't you just angle the neck like you do on most set neck guitars? If it needed to stand proud a small wedge could be added under the F/B extension as is done on archtops. As I recall Melvyn Hiscock does angle his thru neck slightly to get the right geometry.
- Peter Wilcox
- Posts: 1323
- Joined: Sun Jan 08, 2012 1:31 am
- Location: Northeastern California
Re: Neck-through construction geometry
In the only neck-thru I've built, I didn't take the saddle height into serious consideration (and the cheap Chinese bridge/saddle I used had very limited height adjustment), so this was my cringe-worthy solution:
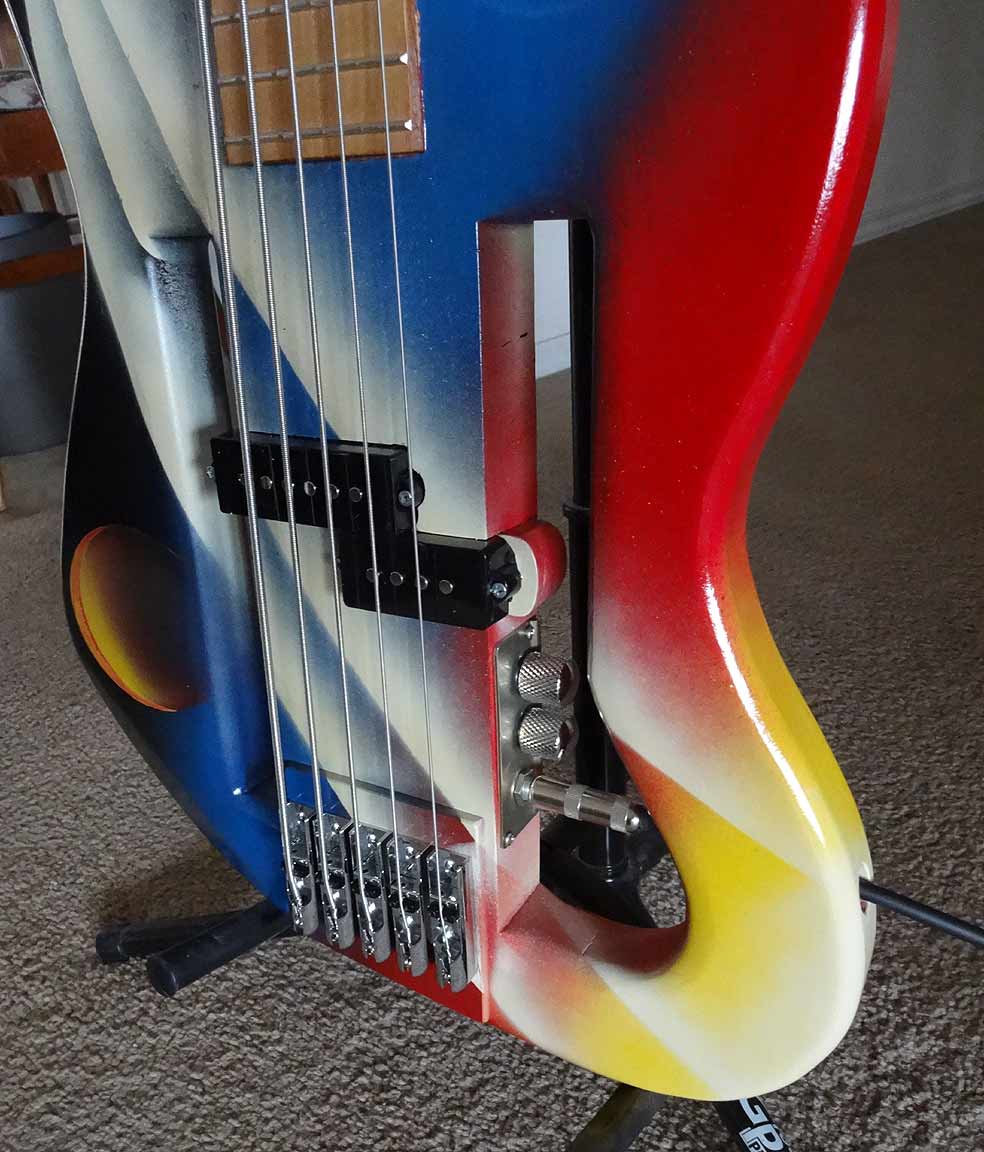
Maybe I can't fix it, but I can fix it so no one can fix it
-
- Posts: 44
- Joined: Wed Jan 11, 2012 2:43 pm
- Location: Catskills area
- Contact:
Re: Neck-through construction geometry
That's great! I really love your cord "strain" relief!
-
- Posts: 1188
- Joined: Wed May 30, 2012 11:47 pm
- Location: Edmonton AB. Canada
Re: Neck-through construction geometry
Here are a couple of pics of a neck through guitar with a 9/32 thick fret board, taken while in construction.
In my opinion, it does not look too thick.


In my opinion, it does not look too thick.


I need your help. I can't possibly make all the mistakes myself!
-
- Posts: 145
- Joined: Mon Jan 20, 2014 7:17 pm
Re: Neck-through construction geometry
I did the same as David. Made the neck beam the thickness required to get the Fingerboard up above body, in my case around 1/2" total , then routed away the portion that passes through the body. I used dowels as registration between neck and body to keep things aligned, worked really well.